In the apparel industry where profit margins are thin and buyers demand ever more sophisticated products and better service, the digitalization has a great potential to drive profit and growth.Unfortunately, unlike other sectors there are not many innovative solutions available for the garment manufacturers. A few solutions that are available are either too costly or so barebone that they fail to meet the dynamic and flexible requirements of the apparel industry
Jaza Software a tech startup by Md Jawed Akhtar and Md Zahid Raza, the young entrepreneurs from two diverse backgrounds- apparel and technology respectively. Based out of Bangalore, the company designs smart software solutions especially for the apparel manufacturing sector with a vision to be the most trusted and reliable partner in the digital transformation journey.
“Since fabric and CM (cost of making) costs are the two major cost components that cover almost 80% of the total FOB price, the cost saving effort should be directed to these areas first. Our flagship software solutions- OptaCut and SPMS (Smart Production Management System) have been designed to target these two areas and cover almost the entire factory digitalization”, said Md Jawed Akhtar, Co-founder & CEO, Jaza Software. Optacut is a fabric optimization software while SPMS is ashop floor digitalization and automation software.
OptaCut
Optacut is an automated, smart, cloud-based, feature-rich, fabric planning and management software with strong focus on team effort. It can save up to 10% fabric through intelligent algorithmic planning at different stages of order processing. Even 2 to 3% fabric saving can result in millions of dollars saving for a medium sized company.
Through OptaCut, fabric saving begins right at ordering stage. Lakhs of meters of fabric go into deadstock annually because of inaccurate consumption & wastage calculation. Optacut estimates accurate amount of fabric for ordering using Predictive Intelligence.
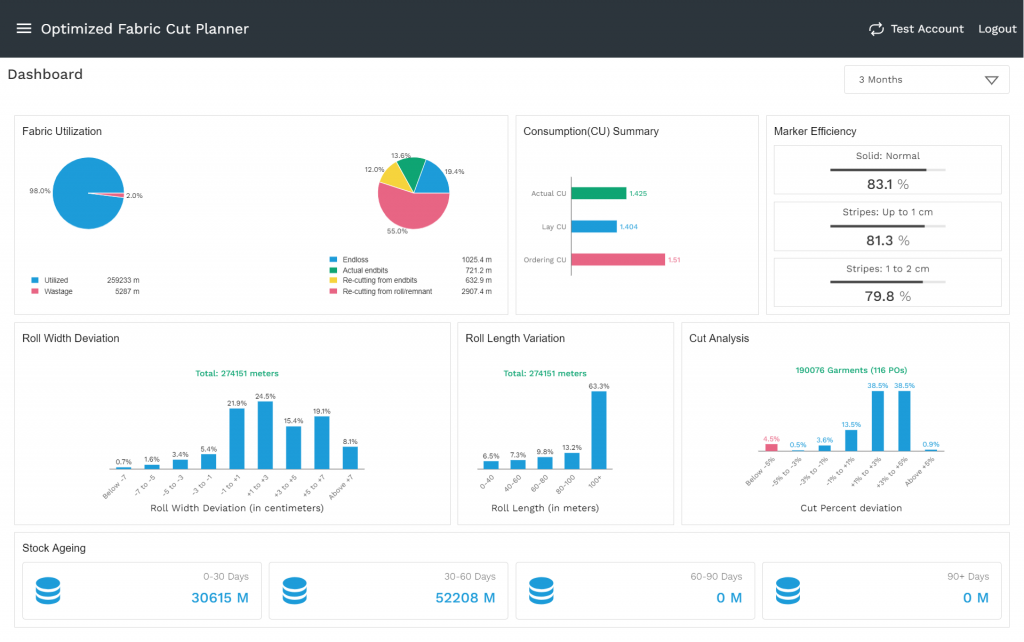
The extent of fabric utilization depends on the quality of cut order plan. Finding the best plan manually out of many possible solutions may not be feasible. “We use almost 15 proprietary algorithms during fabric grouping, ratio planning, ply allocation, and lay slip planning. These powerful algorithms ensure the optimum utilization of fabric minimizing wastages at multiple stages,” added Md Zahid Raza, Co-founder & CTO, Jaza Software.
According to Jawed, “most companies focus only on marker efficiency for optimizing fabric. But this is not enough. There are at least 6 stakeholders who are engaged in the fabric processing. The merchandisers provide information to CAD team for calculating the consumption. Once the consumption is suggested by the CAD team, the merchandisers give the fabric requirement to the sourcing team by adding wastages and buffer. The sourcing team orders the fabric to the mill. When the fabric is received, the warehouse team does inspection and prepares certain reports.Then the CAD team makes cut order plan and finally cutting team executes the plan.”
“Therefore, if you are looking to optimize fabric, then only CAD team cannot achieve this goal. All teams must work together to achieve the common goal. And not only the efficiency but all processes related to the fabric utilization need to be optimized.OptaCut does exactly the same by covering all the steps and bringing all the concerned teams on one single platform with a common goal to increase the fabric utilization,” asserted Jawed.
SPMS: More than a real-time tracking system
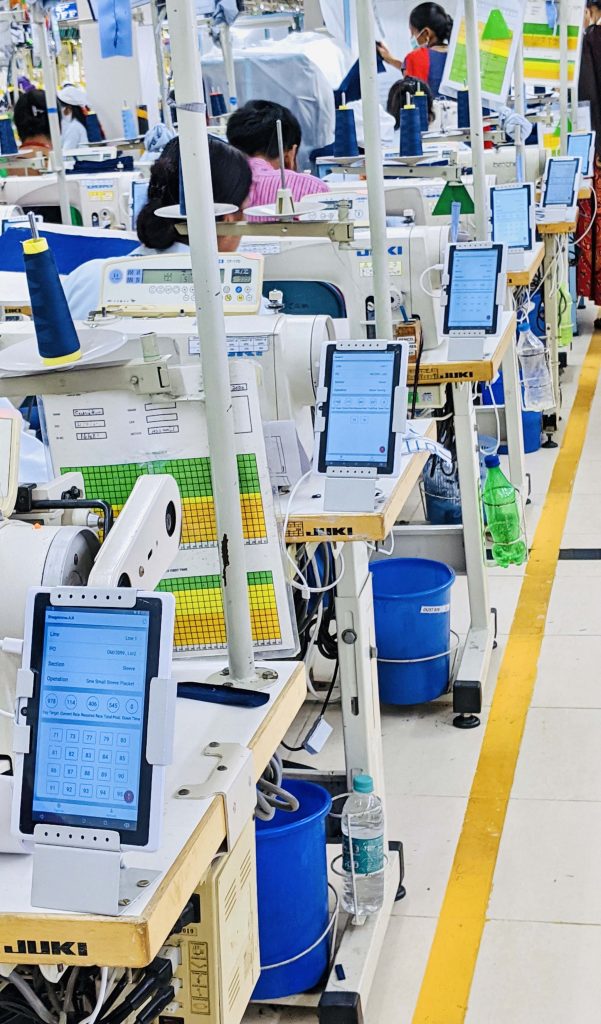
“Whenever we hear about production management software, the first thing that comes to our mind is ‘Real-time tracking system’. It’s a tool which is trending now and has the potential to increase productivity. But do you really think only real-time tracking & reporting alone will increase the productivity substantially and give you a completive advantage?” asks Jawed.
“SPMS is much powerful than the normal production tracking system that can increase productivity 3 times more compared to just a production tracking software,” says a proud Jawed. He further explains how SPMS achieves this by targeting 5 major areas-
Tablet assisted Real-time Tracking
This is the base for the entire solution. A tablet is provided to each operator and helper in the line. It tracks real-time production and efficiency of operators, section, line and the factory. The supervisor and managers can see the color-coded dashboard on a smart TV in each line whereas operators can see their total production and required rate to achieve the day target on their tablets.
The operators are happy because it brings complete transparency where they can see their real performance which is linked to their grades and payroll. Supervisors are happy because they can make quick decision with the real-time data and increase their line efficiency. It’s win-win situation for everyone. The ultimate result is increased productivity.
Automated Work Allocation
Before a style is loaded into a line, the IE team makes a manning(work allocation) sheet. During this there are so many constraints like Operators Skill Matrix, Operators Attendance, Operation Bulletin, WIP, output required, no of workstations, etc. Considering all these factors, there can be millions of possibilities for planning. Manually, it’s very difficult to find out the best solution with maximum efficiency.
SPMS automate this process using algorithms to optimize the efficiency. Planning can be done within minutes with much better efficiency.

Live Line Balancing
After the manning sheet is made, line balancing is again doneevery morning to account for the operators’ absenteeism. But this will not guarantee better efficiency throughout the day. Line balancing is a continuous process. The software tracks live WIP between each workstation, operator performance, downtime, etc. Based on these data software can predict bottleneck in advance and sends alert to the supervisor along with possible solutions.
Smart Andon System to reduce Downtime
One of the main reasons for production loss is downtime. And the worst part is that accurate data is not available to take any concrete action.
Jaza Software has a unique solution for this. They have taken the concept of Andon System to a new level and made an android application where operator raises the issue through a simple touch on the tablet. Now the concerned person who is supposed to solve that problem will receive notification. The time taken to solve the problem is automatically recorded. Now, the data for problem-wise, department-wise downtime is available on the dashboard. This is how they identify the source of problem, quantify it and discourage it through a transparent review mechanism. The net result is less downtime and increased productivity and efficiency.
Smart Quality Management System to reduce Re-work and improve quality
There is quality module also in this system. Each checkers at the end of part sections and assembly sections are given tablets and defects are captured in real-time. From this data DHU report is compiled, alerts for high risk operations, poor performing operator, etc. are sent to concerned persons. Decision can be taken in real-time to bring down the re-work rate.

It also gives alerts and suggestions for critical operations before loading the style into a line based on the past data analysis through predictive intelligence.
“Apart from these two flagship solutions we have a few more solutions and some are in the development and R&D stage also. Digitalization is a continuous process. This isn’t a project with a start and end date. Technology will continue to evolve and call for adaptations to current processes, which means you need to keep learning and evolving. We want to a be the leading supplier for innovative digital solutions to the apparel industry and be reliable partner in their digital transformation journey.” winds up Jawed.